The Influence of Welding Inspection Milwaukee on Project Success and Conformity
Comprehending the Significance of Welding Evaluation in Ensuring Structural Stability and Security Across Numerous Industries
Welding examination is an indispensable procedure that safeguards architectural stability and safety and security throughout varied industries. As we check out the details of welding inspection, the concern occurs: what are the most essential elements that contribute to effective assessment processes?
Function of Welding Examination
While the stability of welded frameworks is paramount to safety and efficiency, the role of welding examination can not be overemphasized. Welding examination acts as a crucial quality assurance process that ensures the adherence to established criteria and specs throughout the welding operation. By systematically assessing welds for flaws, disparities, and non-compliance, examiners play a vital function in guarding the integrity of frameworks throughout numerous markets.
Welding evaluations incorporate a series of activities, from pre-weld assessments to post-weld evaluations. These evaluations not just recognize possible concerns prior to they intensify but also enhance the overall dependability and lifespan of bonded parts. Welding Inspection Milwaukee. Inspections help to validate the ability and competencies of welders, making sure that welding procedures are performed properly and products work
Moreover, a strenuous inspection procedure promotes compliance with governing requirements and market criteria, minimizing the risk of tragic failures. By promoting a society of security and accountability, welding examination adds considerably to both operational and economic efficiencies. In amount, the function of welding assessment is crucial, as it underpins the top quality, safety, and long life of welded structures important to modern framework and market.
Kinds Of Welding Inspections
Understanding the different kinds of welding evaluations is vital for keeping the quality and security of welded frameworks. Welding evaluations can be classified right into a number of types, each serving a details objective in the analysis process.
Visual evaluation is the most basic type, involving a careful exam of the welds with the nude eye or through zoom. This approach aids determine surface area issues such as fractures, incomplete fusion, or too much spatter.
Next is non-destructive testing (NDT), which consists of techniques such as ultrasonic testing, radiographic screening, and magnetic bit screening. These methods enable examiners to assess the honesty of welds without jeopardizing the product's framework. Ultrasonic screening uses high-frequency acoustic waves to discover interior defects, while radiographic testing utilizes X-rays or gamma rays to imagine inner weld attributes. Magnetic fragment testing, on the other hand, is reliable for finding surface and near-surface stoppages in ferromagnetic materials.
Devastating screening, though much less typical, entails physically evaluating samples to recognize the weld's mechanical residential or commercial properties. Each sort of examination contributes to an extensive evaluation, making certain that welding satisfies market requirements and safety needs.
Sector Criteria and Regulations
Developing sector requirements and laws is essential for ensuring the security and integrity of bonded frameworks. These standards function as benchmarks for top quality, efficiency, and safety and security, assisting manufacturers and inspectors in the execution of welding procedures. Different organizations, such as the American basics Welding Culture (AWS) and the International Company for Standardization (ISO), have actually established thorough criteria that determine procedures for welding practices, qualification of welders, and inspection techniques.
Compliance with these laws not just boosts the quality of welds yet also minimizes threats connected with structural failings. Certain codes, such as the ASME Boiler and Stress Vessel Code, overview demands for the building and construction of pressure vessels, ensuring they can withstand functional stresses. Furthermore, regional and nationwide guidelines commonly mandate adherence to these industry criteria, reinforcing their relevance throughout fields like building and construction, aerospace, and automobile manufacturing.
Normal updates to these criteria mirror improvements in modern technology and welding methods, making sure that safety and security steps continue to be relevant. Therefore, a detailed understanding and implementation of these criteria is important for welding professionals, fostering a society of safety and security and top quality in welded frameworks.
Effects of Poor Inspections
Insufficient inspections can lead to extreme effects in the welding industry, undermining the very standards and laws designed to ensure security and architectural integrity. The effects of bad assessments can materialize in different types, from prompt safety hazards to lasting architectural failings.
In addition, poor evaluations can stain a company's online reputation and result in legal consequences, including penalties and lawsuits. Eventually, the implications of bad assessments prolong past specific tasks, impacting industry-wide standards and public assumption, thus stressing the vital need for rigorous and reliable welding evaluations.
Finest Practices for Effective Inspections
Efficient welding evaluations are extremely important to guaranteeing the integrity and safety of bonded structures. To achieve ideal outcomes, assessors need to abide by several finest practices that improve the inspection procedure.
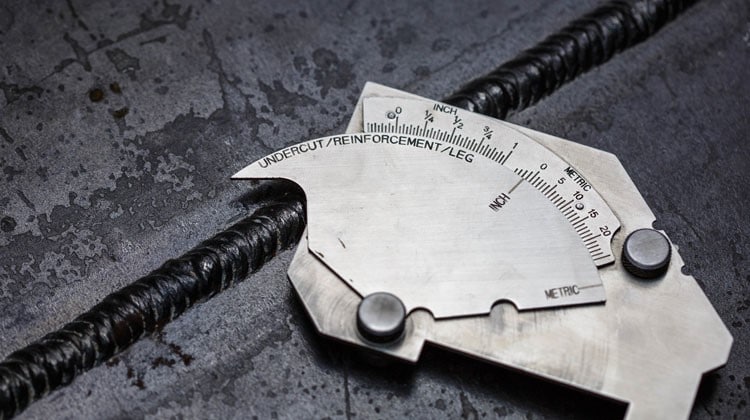
Second of all, assessors must possess the needed certifications and accreditations relevant to the welding processes and materials being analyzed. Ongoing training and professional development are vital to staying upgraded my link on industry standards and technological advancements.
Additionally, using ideal assessment devices and strategies, such as aesthetic inspections, ultrasonic testing, and radiographic examinations, is vital for detecting flaws that might jeopardize architectural stability.
Finally, thorough documentation of the inspection process is necessary. This includes recording findings, photos, and any rehabilitative activities taken. Clear and specific reporting not only facilitates liability yet also aids in future assessments and upkeep. By executing these finest techniques, companies can significantly boost the efficiency of their welding assessments and ensure risk-free, trusted procedures.
Verdict
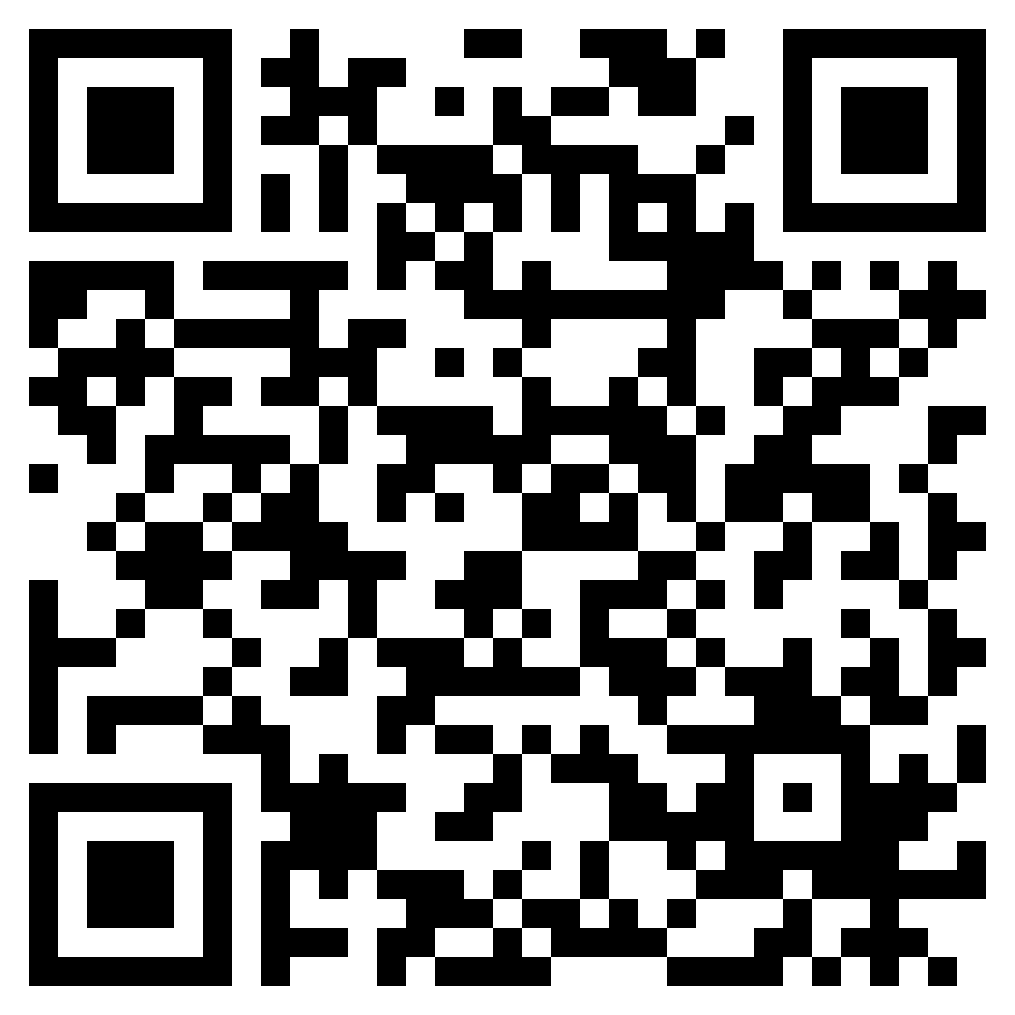
In conclusion, welding inspection is crucial for preserving architectural honesty and safety and security across various markets. Prioritizing reliable welding assessments is crucial to guarantee the safety and security of workers, properties, and general functional integrity.
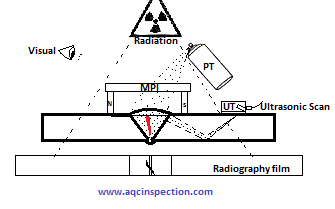
As we check out the intricacies of welding evaluation, the concern occurs: what are the most vital factors that contribute to effective inspection processes?
Welding examination serves as an important top quality control wikipedia reference process that guarantees the adherence to developed standards and specifications throughout the welding operation. In sum, the function of welding inspection is important, as it underpins the top quality, safety and security, and longevity of bonded structures vital to modern-day infrastructure and market.
Various companies, such as the American Welding Culture (AWS) and the International Company for Standardization (ISO), have established detailed criteria that determine treatments for welding methods, certification of welders, and examination techniques.
Inevitably, the implications of inadequate assessments expand past private jobs, impacting industry-wide requirements and public assumption, hence stressing the critical demand for rigorous and effective welding examinations.